A 2015 Ford F-350 equipped with the 6.7L Power Stroke diesel and 6R140 automatic transmission arrived at our shop with a customer complaint of harsh shifting. According to the referring shop, the vehicle had just received a replacement transmission, but the symptoms persisted exactly as before. The customer noted that the harsh shift - specifically from 1st to 2nd - had been an ongoing issue for over a year and had already been through multiple shops and repair attempts.
Initial ObservationsUpon receiving the truck, the first step was a full diagnostic scan, which returned no active trouble codes. This alone raised an eyebrow, as the reported symptoms were severe enough that one might expect at least a gear ratio or shift error code.
During a road test under light throttle, the scan tool showed the TCM (Transmission Control Module) commanding a shift into 2nd gear, but the actual shift event lagged by four to five full seconds. When the shift finally occurred, it was abrupt and forceful - harsh enough to break rear-wheel traction. Interestingly, under heavier throttle (approximately 3/4 to full), shifts executed normally with no perceptible delay or harshness. Switching the truck into manual shift mode produced the same delay under light throttle conditions.
The lack of diagnostic trouble codes despite such an exaggerated delay was puzzling. Given that a freshly rebuilt transmission had already been installed, we needed to determine whether the root cause was inside the transmission or elsewhere in the vehicle's control system.
Digging into the Electrical SideTo isolate the problem, we clamped an inductive amp probe over the 1-2 shift solenoid wire. What we found was telling: the TCM was taking several seconds to send the activation signal to the solenoid after commanding the shift. This confirmed the issue wasn't mechanical or hydraulic inside the unit - it was electronic, and upstream of the transmission itself.
We then verified the solenoid body strategy programming. The calibration ID on the side of the replacement transmission did not match the TCM's stored solenoid strategy. To eliminate this mismatch, we reprogrammed the strategy using Ford's FJDS diagnostic tool. While connected, we also performed a full reflash of the TCM software to rule out any firmware-related issues and followed up with a KAM (Keep Alive Memory) reset and adaptive parameter reset.
After performing another road test, the problem persisted exactly as before. Clearly, the issue was not due to a programming or adaptation error.
Considering the Truck's ConditionAt this point, we took a step back to consider the broader picture. The truck had over 300,000 miles on it, had been tuned and emissions-deleted, and had already seen replacement of major drivetrain components. With that kind of age and mileage, wiring degradation becomes a strong possibility.
A visual inspection of the TCM connector revealed a severely corroded 12V power supply wire. We repaired the corroded terminal and replaced the damaged pin, expecting at least some improvement. Unfortunately, the shift delay remained. (Figure 1)
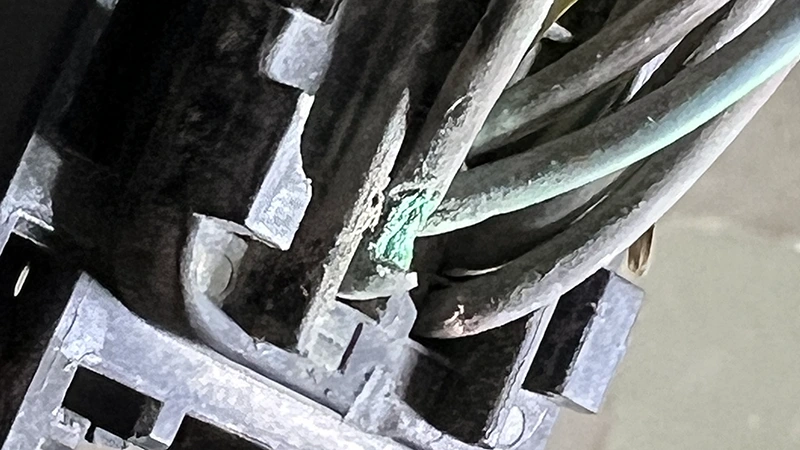
Figure 1
At this point, we contacted the referring shop for a full background on previous work. They informed us that they had already tried replacing the valve body, swapping in both a new and a used TCM, replacing the entire transmission assembly, and even installing a known-good PCM (Powertrain Control Module) from another truck. Still, the issue had persisted.
Knowing how many components had been changed and verified ruled out most of the usual suspects. It was time to scrutinize the data more deeply - specifically engine-side PID (Parameter ID) data that might be affecting shift timing indirectly.
Analyzing the DataWe reviewed the live data from the transmission controller again: commanded gear, actual gear, input/output speed sensors, turbine speed - all readings were within normal parameters, and no errors were present. Line pressure tests with a mechanical gauge also looked healthy across all ranges, with one exception: during the delayed shift, pressure kept climbing excessively with rising RPM, culminating in a violent engagement into 2nd gear.
We moved our focus to powertrain-related sensors. Speed sensors, ABS, yaw rate, steering angle - all were functioning correctly. Then, we examined the engine control side and noticed something unusual. During light throttle acceleration, the exhaust back pressure (EBP) sensor showed a sudden and unexplained spike. On the delayed 1-2 shift, the EBP signal would climb to 474.2 kPa (68.8 psi) - a value far higher than expected during mild acceleration. (Figure 2)
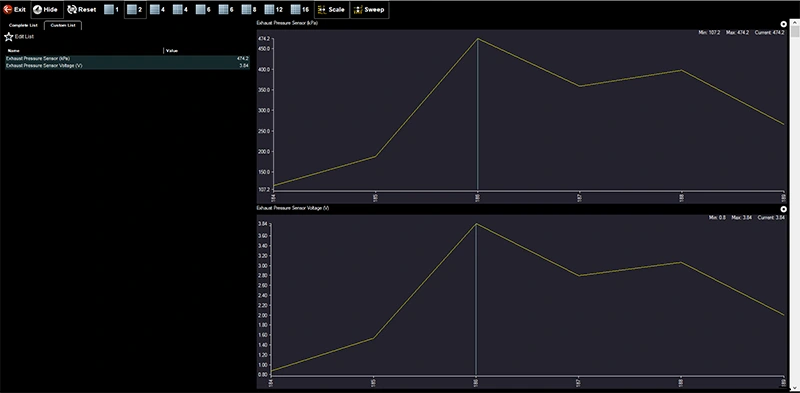
Figure 2
We contacted a local diesel specialist to confirm expected EBP readings. They confirmed that under normal light-load acceleration, EBP values should be well below 30 psi. The extreme spike we observed indicated that the PCM was likely interpreting a falsely elevated engine load condition.
We installed a new EBP sensor sourced directly from Ford and took the truck out for another road test. (Figure 3)
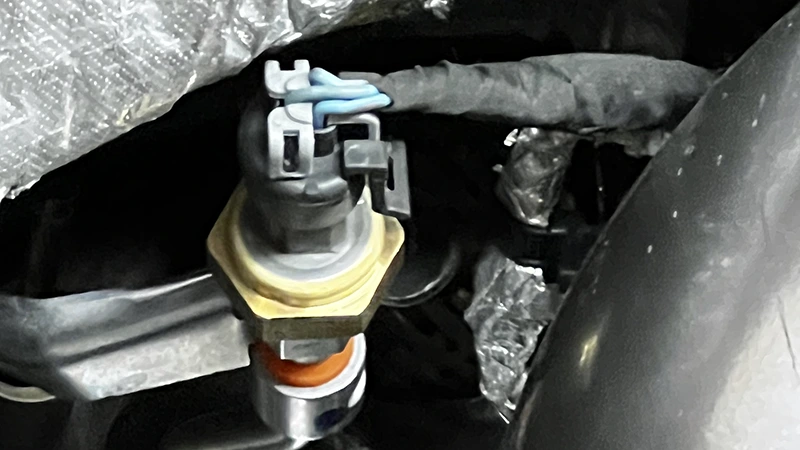
Figure 3
The results were immediate: the 1-2 shift occurred smoothly and on time. The new sensor produced maximum EBP readings of 206.3 kPa (29.9 psi) under heavy acceleration - well within expected parameters. The harsh shift was gone, and drivability was restored. (Figure 4)
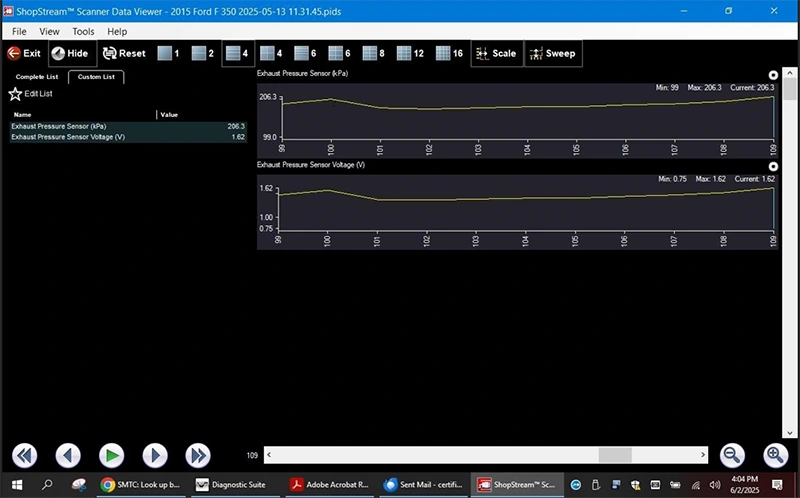
Figure 4
This repair was anything but straightforward. What initially presented as a classic internal transmission failure turned out to be an indirect control issue caused by a faulty exhaust back pressure sensor. While this sensor is not typically associated with transmission shift timing, its input - especially under altered calibration or tuning - can mislead the PCM into interpreting a high-load scenario. The result? Adjusted shift timing, higher commanded line pressure, and ultimately a harsh shift.
This case underscores the importance of a holistic diagnostic approach, especially on modern vehicles where multiple control modules share data and influence each other's behavior. It's a reminder that not all transmission problems are transmission problems. Sometimes, it's the sensors and signals outside the unit that create the illusion of an internal fault.
The customer, who regularly tows a large camper, was understandably relieved. After more than a year of frustrating repairs and replacements, his truck finally drove the way it was supposed to. For us, it was a valuable lesson in persistence, patience, and never ruling out the "unlikely" until it's been checked.